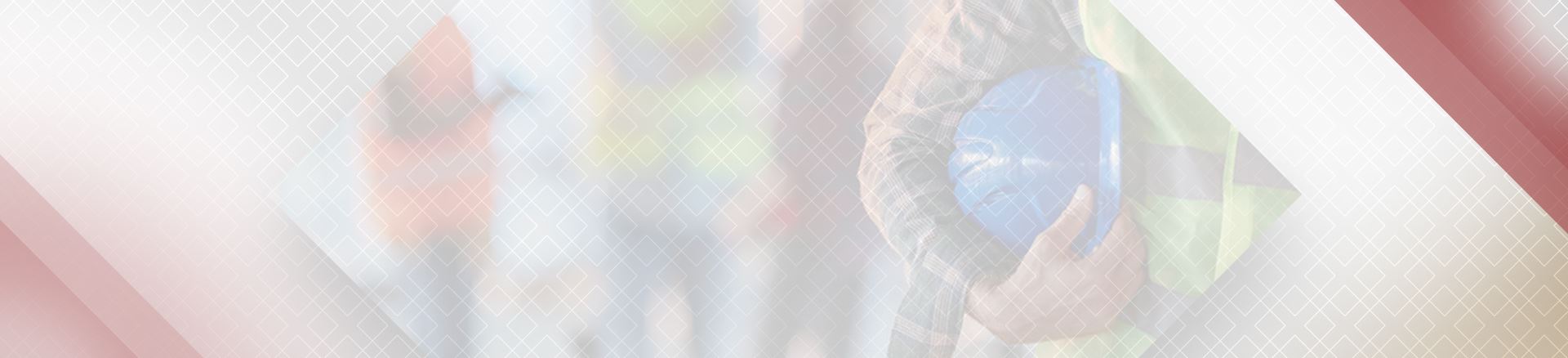
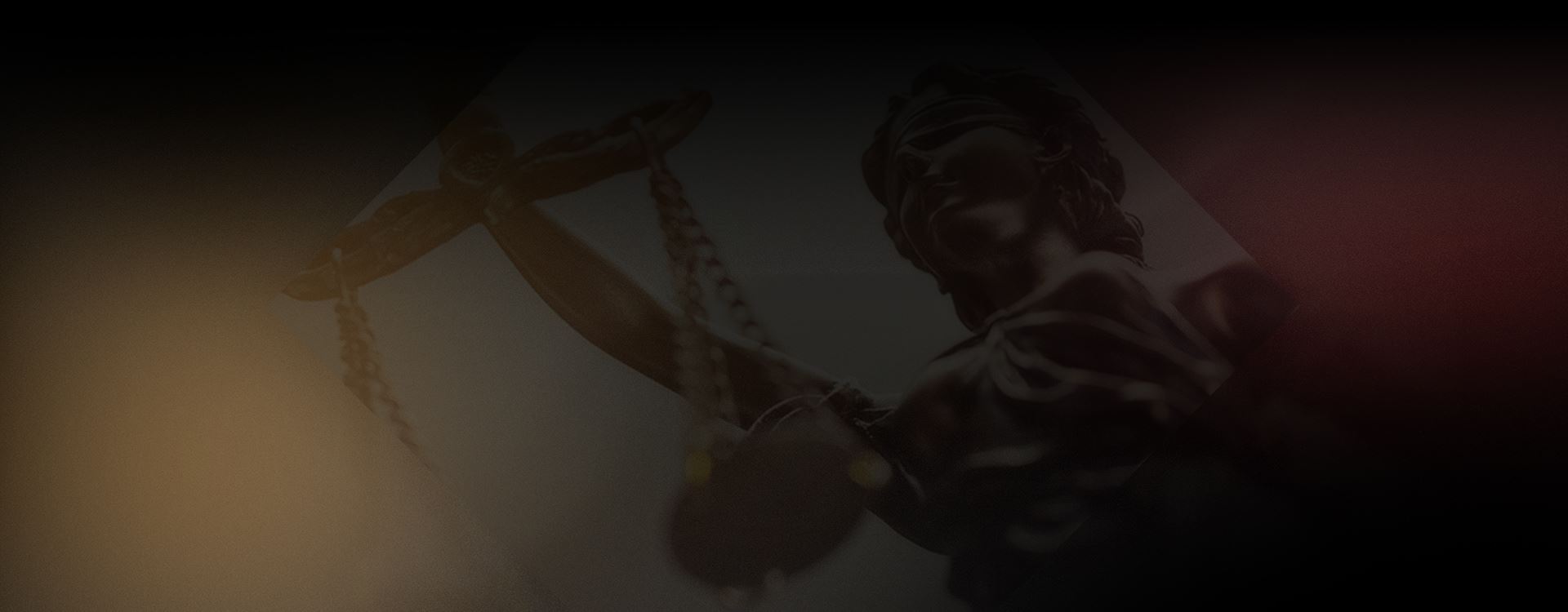
Relentlessly Pursuing the Best Possible Outcome
We've Recovered Hundreds of Millions for Our Clients
-
$30m Product Liability Verdict
-
$24m Wrongful Death Settlement
-
$14m Medical Device Settlement
-
$13.5m Personal Injury
-
$12m Child Wrongful Death
-
$11m Personal Injury
Common Types of Industrial Accidents Caused by Poor Maintenance
Industrial accidents caused by poor maintenance can be particularly hazardous due to the heavy machinery, complex systems, and hazardous materials often involved in industrial settings. Here are some common types of industrial accidents that can result from inadequate maintenance:
- Machinery Malfunctions: Poor maintenance of machinery can lead to equipment failure or malfunction, causing unexpected stoppages or erratic behavior that puts workers at risk. Safety devices and guards may not function properly, increasing the danger of contact with moving parts.
- Electrical Accidents: Inadequate maintenance of electrical systems can result in short circuits, leading to fires, explosions, or electrocution. Arc flashes caused by faulty equipment can cause severe burns or other serious injuries.
- Slip, Trip, and Fall Accidents: Neglecting to maintain walking surfaces can create hazards like slippery floors or uneven ground, leading to slips, trips, and falls. Such accidents are common when leaks or surface damage go unrepaired.
- Chemical Spills and Leaks: Poor maintenance of seals, valves, and containment systems can cause hazardous chemical leaks or spills. These incidents can lead to dangerous exposure, burns, or environmental harm.
- Structural Failures: In industrial settings, poorly maintained structures, such as scaffolding or beams, can collapse, endangering workers. Falling objects from unstable storage racks or overhead structures also pose significant risks.
- Fire Hazards: Fire prevention systems require regular maintenance; otherwise, faulty equipment can lead to uncontrolled fires or explosions. In environments with flammable materials, poor ventilation system maintenance can increase explosion risks.
- Conveyor System Accidents: Conveyor systems can become hazardous if not properly maintained, leading to jams, blockages, or belt failures. These issues can cause sudden stops or unexpected movements, endangering workers nearby.
- Forklift and Vehicle Accidents: Industrial vehicles like forklifts need consistent maintenance to ensure safe operation. Brake failures or steering malfunctions due to poor upkeep can result in collisions or loss of control, leading to serious accidents.
- Pressure Vessel Explosions: Pressure vessels, such as boilers, must be regularly maintained to prevent overpressure and potential explosions. Malfunctioning safety valves or relief systems can cause catastrophic failures.
- Crane and Hoist Accidents: Cranes and hoists require regular inspections and maintenance to prevent load drops or mechanical failures. Neglecting this upkeep can result in serious injuries or fatalities during lifting operations
Maintenance is crucial in any industrial setting for several key reasons:
- Safety: Regular maintenance ensures that equipment and machinery function correctly, reducing the risk of malfunctions that can lead to accidents and injuries. Well-maintained systems and safety devices help protect workers from harm and prevent hazardous situations.
- Operational Efficiency: Proper maintenance keeps equipment running smoothly, minimizing downtime and preventing costly breakdowns. Efficiently operating machinery ensures that production processes are reliable and that output levels remain consistent.
- Cost Savings: Investing in regular maintenance can prevent expensive repairs and replacements by addressing issues before they escalate. This proactive approach can also extend the lifespan of equipment, providing long-term financial benefits.
- Compliance: Many industries are subject to regulations and standards that require regular maintenance and inspections. Adhering to these requirements helps avoid legal issues and potential fines, ensuring that operations remain compliant with safety and environmental regulations.
- Quality Assurance: Maintained equipment performs more consistently, which helps ensure the quality and reliability of products. Preventing defects and ensuring that machinery operates within specified tolerances can enhance product standards and customer satisfaction.
- Operational Continuity: Scheduled maintenance helps avoid unexpected breakdowns that can halt production and disrupt operations. By planning and executing regular maintenance, businesses can minimize interruptions and maintain smooth workflow.
- Energy Efficiency: Well-maintained machinery often operates more efficiently, consuming less energy. Regular maintenance can help identify and rectify issues that lead to energy waste, contributing to overall operational sustainability and cost reductions.
- Employee Morale: A safe and well-maintained work environment positively impacts employee morale and productivity. Workers are more likely to feel valued and motivated when they operate in a safe, reliable, and efficiently running environment.
Severe injuries can require prolonged hospital and medical treatment and may cause temporary or permanent disability. An insurance settlement may be insufficient to compensate for a terrible accident that causes the victim to suffer physically and emotionally.
In the last 14 years, Shoop & team's impressive track record includes hundreds of Product Liability cases resulting in verdicts or settlements exceeding $1 million. For a Product Liability team with an exemplary track record, clients choose Shoop.

Consult With an Experienced Industrial Machinery Accident Lawyer
David Shoop and the other experienced attorneys at our firm work closely with each client following an injury accident to ensure he or she receives the best possible legal representation. It is best to speak with an attorney before settling with an insurance company. There may be further monetary compensation available from an industrial accident caused by poor maintenance of machinery. Make an appointment today for a consultation and case evaluation.
Contact a Los Angeles Harbor Industrial Machinery Accident Lawyer for compensation for injuries caused by poor maintenance.
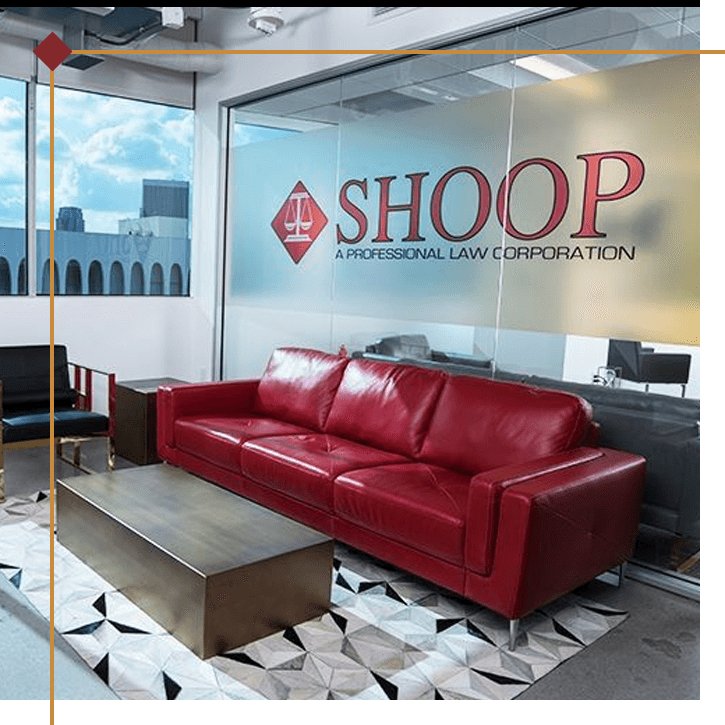
